At the factory, where LCD monitors and visual solutions are manufactured, EIZO has installed its very own IP decoding monitor and box solutions that are connected to IP cameras for keeping eyes on production processes and ensuring employee safety. Introducing these solutions now allows EIZO to maintain visibility of the production floor in real time, which provides many benefits as a result.
DuraVision Referenz
Full overview in production
EIZO installs its own IP decoding solutions to maintain visibility of production processes
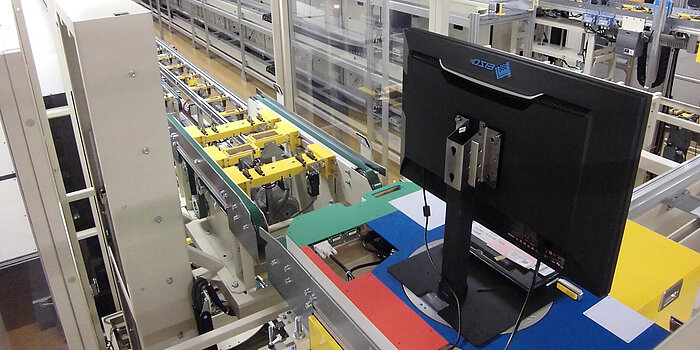
Advantage of the installation: Securing employees remotely
Improving visibility in the restricted access cleanroom
The EIZO factory has its own ISO Class 1* cleanroom where touch panel monitors and other sensitive products are manufactured. Class 1 is the highest classification of ISO 14644-1, and to maintain the strict cleanliness standard, only a small number of employees are allowed in the area. This access restriction made it difficult to monitor production and the safety of the employees inside.
*ISO 14644-1 Class 1 specifies a maximum particle concentration of 0.1 micrometre per 1 m3 of air.
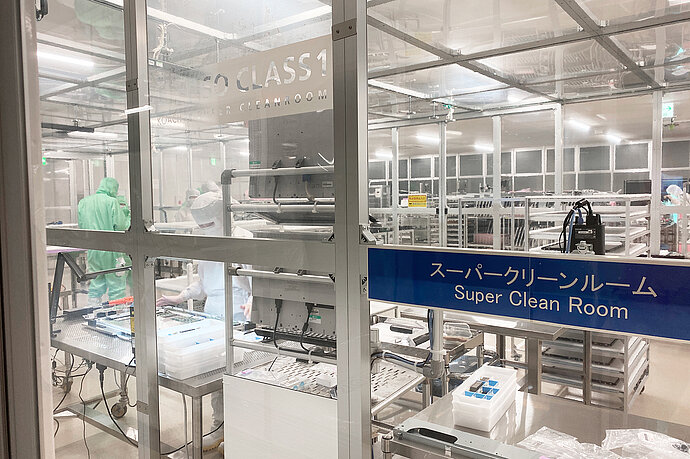
Clean room from the outside
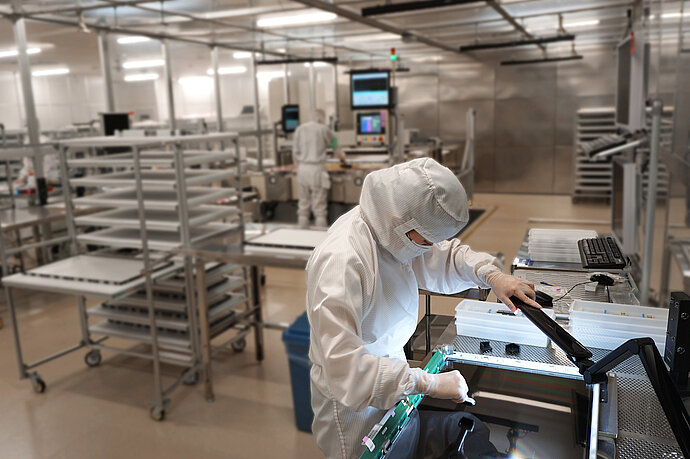
Working in the clean room
This is where the DuraVision FDF4627W-IP comes in - this large 46-inch IP decoding monitor was installed in the management office which enabled supervisors to check on progress and monitor worker safety from outside the clean room.

46" IP decoding monitor in the management office
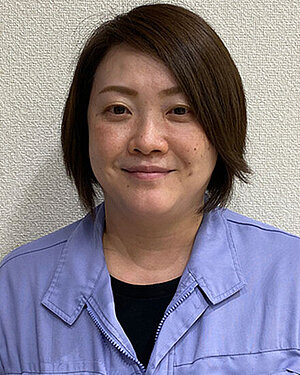
"The cleanroom is not an area that we can easily enter and leave, so it is incredibly useful for us to be able to track production by looking at what's on the screen. It helps us with process control."
Yuka Wakabayashi
Leader Manufacturing Department, EIZO Corporation
Advantage of installation: Improved visibility of unmanned processes for efficient staff deployment
Tracking difficult operating conditions
EIZO uses an automatic inspection system that employs artificial intelligence (AI) in the monitor production process.
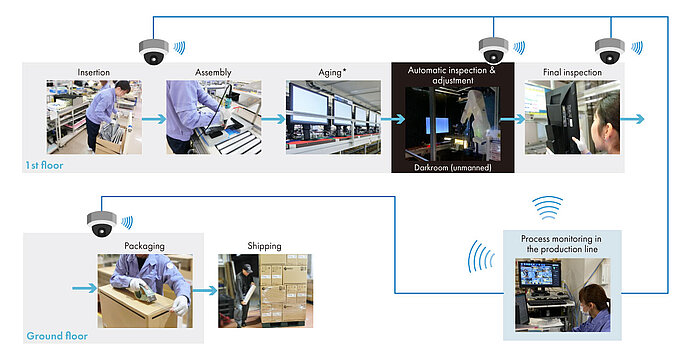
*A procedure in which the monitor is left on for an extended period of time to achieve and verify a stable operating condition.
As the inspection process takes place in an unmanned darkroom, production staff cannot enter the room at any time to monitor the process. To solve this problem, EIZO installed an IP camera inside the inspection room, connected to the DX0211-IP IP decoder box and a 31.5-inch 4K monitor mounted outside the room. Computerless, with only a LAN connection between the camera and the IP decoder box, the monitor displays images from the inspection room. This allows EIZO to detect and resolve anomalies at an early stage and reliably maintain smooth operation.
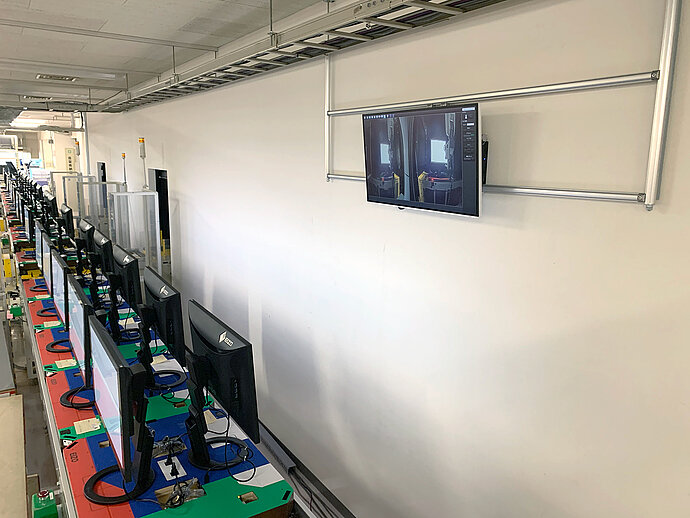
31.5" UHD 4K monitor provides view of the unmanned inspection room
Advantage of the installation: Efficient observation of production processes
Monitoring of process chains with spatial separation
Automated processes that use AI complement the production processes at EIZO. Since they are usually unmanned, IP decoder monitors are installed at operations that follow automated production steps, for example where employees visually inspect the products.
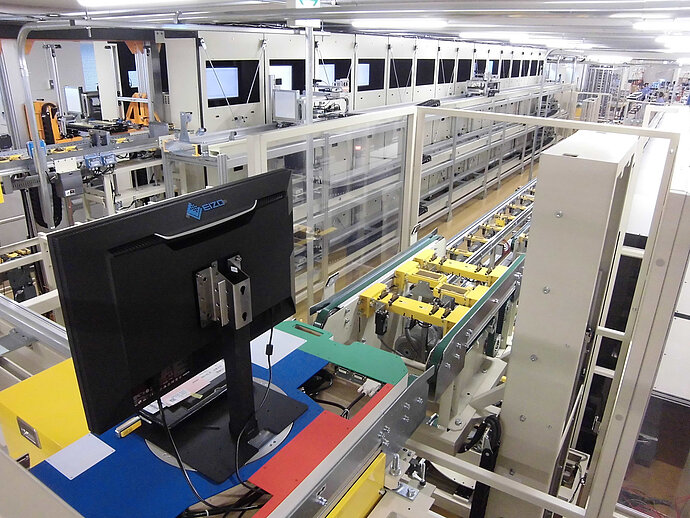
State-of-the-art automated production process
Although the assembly, inspection and packaging processes span several floors, production staff can easily check the progress of the previous process, make appropriate staffing adjustments, and respond effectively to backlogs, all resulting in improved production efficiency.
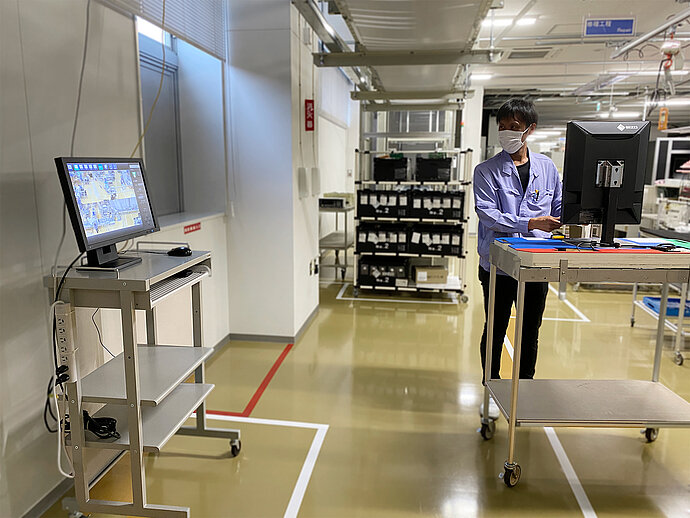
Observation of automatic processes during ongoing production
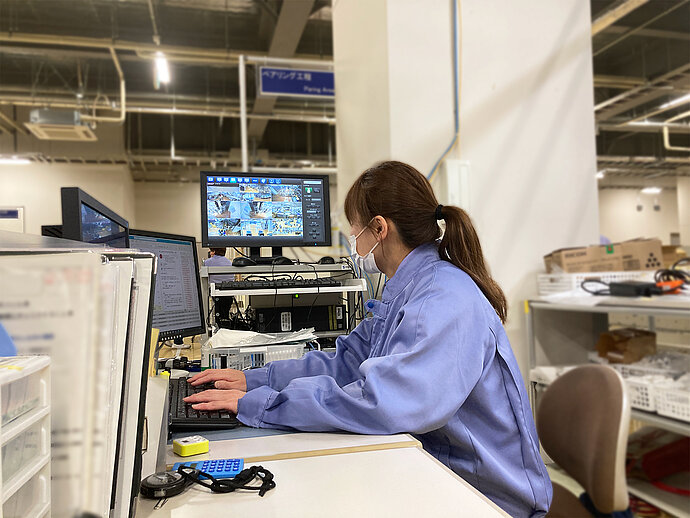
Checking the production line on another floor via the monitor
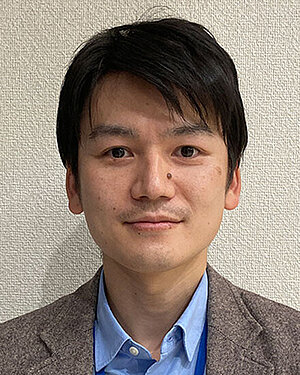
"The IP decoding monitors and the IP decoding boxes can easily contribute to improved production monitoring. We are proud to use our own products. The ease of being able to view live video from IP cameras by simply connecting via LAN and without a PC is invaluable."
Shinichi Yasukawa
Section Manager Manufacturing Department, EIZO Corporation
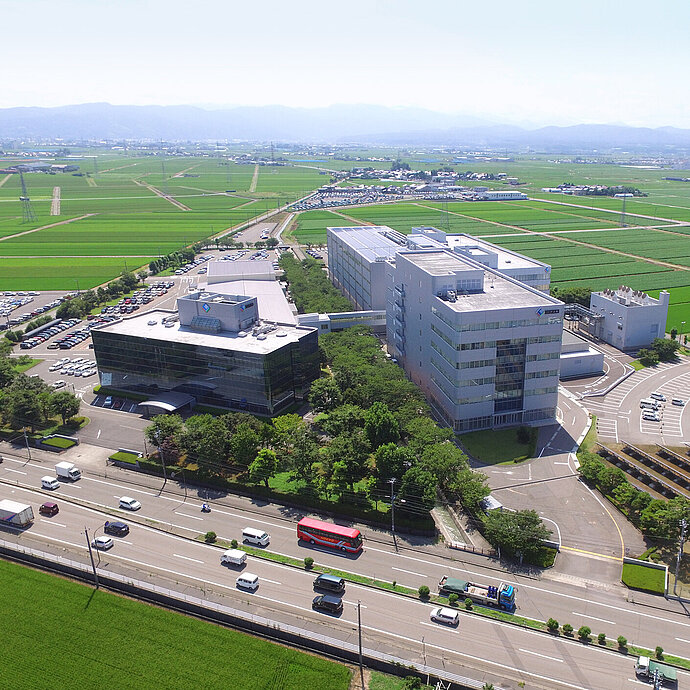
EIZO headquarters in Japan
EIZO's headquarters are located in the city of Hakusan, Ishikawa Prefecture, Japan. This is where planning, development, quality control, manufacturing and after-sales service for the various product lines come together. This unique integration enables EIZO to provide high-quality solutions to users around the world.